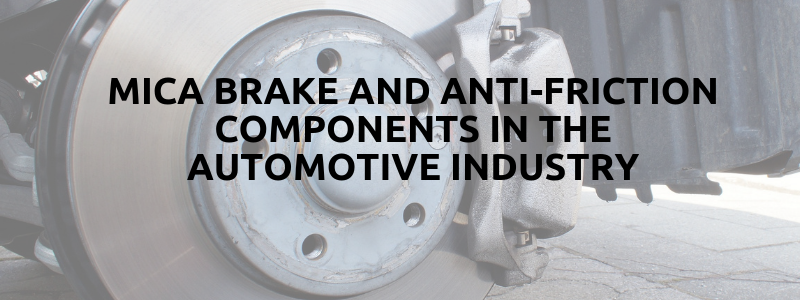
Mica Brake And Anti-friction Components In The Automotive Industry
It should go without saying that brakes are critical car parts. Our manufacture and supply of mica brake and anti-friction components are part of how we support the automotive industry.
Any mechanical process should start smoothly and to run effectively. It must also be able to stop or slow down safely, within accepted parameters and technical specifications.
To ensure processes can do this, manufacturers rely on the brake and anti-friction components. These components comprise friction materials.
In this blog, we will look at friction, what can be done to manipulate it, and how mica contributes to braking systems in vehicles.
How Friction Works
Friction is the resisting force when there is sliding motion between surfaces. It applies anywhere where surfaces come into contact with one another.
As a force, friction acts in the opposite direction to the way an object is sliding or moving.
There are two main physical aspects friction has controlling it:
- how sticky the sliding surfaces are; and
- how much of an impression is made on the surfaces by them rubbing together.
For example, early humans were able to make fire by rubbing surfaces together, typically hardwood against softwood. As we will see, the combustibility of friction materials is a key concern when it comes to the manufacture of vehicles.
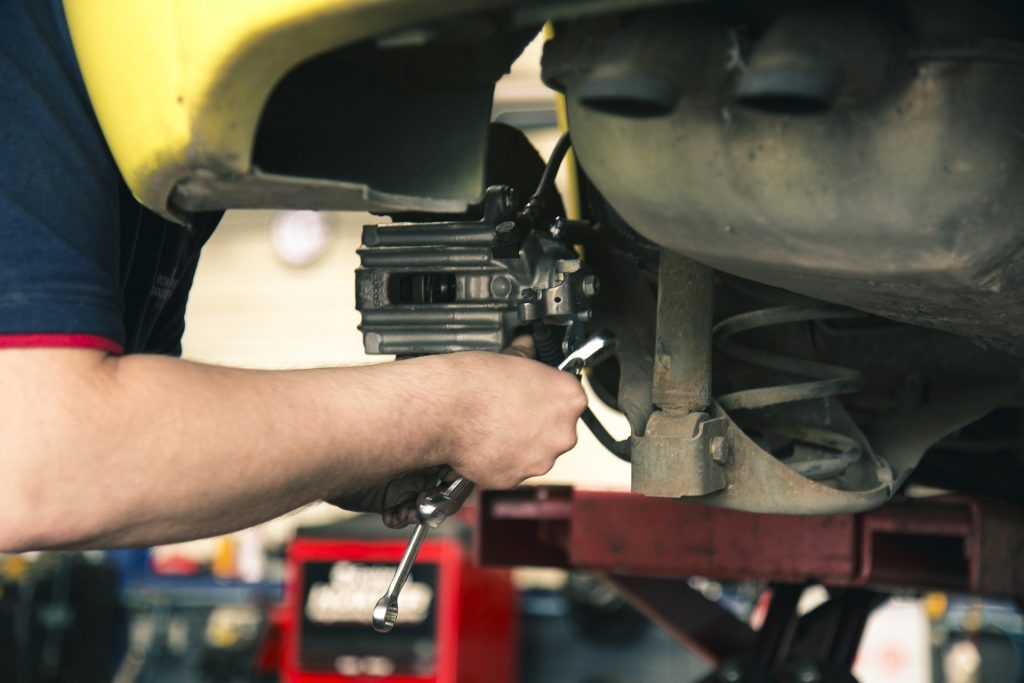
Friction And Thermal Energy
One of the by-products of creating friction is heat, or thermal, energy.
Newton’s Second Law is concerned with unbalanced forces. They produce an acceleration, and the greater the unbalanced force, the greater the acceleration.
Unbalanced forces generally occur when a forward force, or thrust, and a frictional force work against each other. The kinetic energy you get when two surfaces move like this over each other can create thermal energy.
Consequently, manufacturers will typically use heat-resistant materials as friction materials.
In 1888, Bertha Benz, a German, invented brake pads, as one of the earliest long-distance drivers. These early brake pads were made from asbestos, as an effective heat-resistant material.
Nowadays, asbestos is widely recognised as posing a potentially deadly health risk. This means the automotive industry has had to find alternatives for friction material.
Friction Materials
Ceramic has proved to be a popular alternative to asbestos, but modern frictional materials can also be a combination of raw materials with modifiers and reinforcements.
The base raw material will have a strengthening bonding material added, usually a resin, then there will be an additional stiffener material to make the friction material even more durable.
These stiffener materials can be various organic and inorganic fibres, including metals and synthetic polyamides such as aramid.
One organic raw material that is an effective friction material is mica.
Mica has natural mineral properties which make it ideal as a dielectric insulator while being both hardwearing but also highly adaptable. It provides thermal protection that is essential to friction materials in the automotive industry.
Brake And Anti-friction Components
Brake and anti-friction components are brake pads and brake linings. The quality of these components will vary, depending on the manufacturing process and on the materials they are made from.
In the European automotive industry, generally, these components are made from low-steel friction materials. This is because braking at high speeds is a relatively common occurrence.
Non-steel brake pads strike the right balance between strength, effectiveness and resistance to brake-squeal – the continuous, high-pitched sound you get when brake pads have worn down.
Other brake and anti-friction components in automotive braking systems are:
- friction discs – metal plates bonded with friction material
- clutch discs – linking a car engine to its transmission input shaft
- clutch facings – assisting the clutch in starting and stopping the flow of energy
- brake linings – lining brake shoes, the metallic part of braking systems.
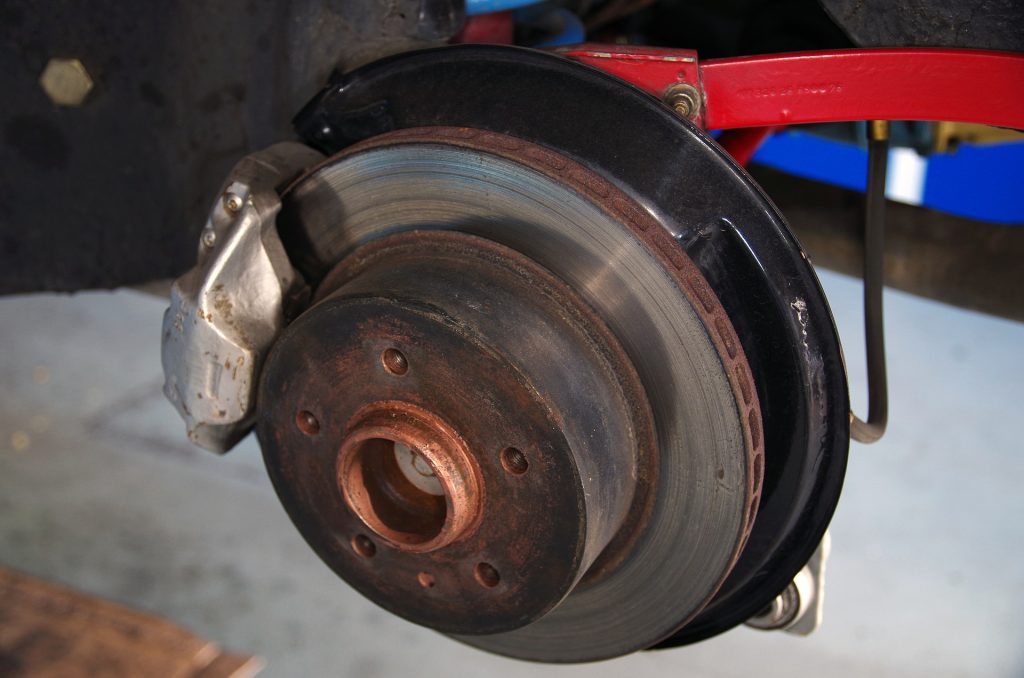
Meeting Performance Requirements
Friction materials should demonstrate performance alongside quality, extending the service life of brake and anti-friction components in vehicles.
In manufacturing, a dynamometer measures torque and rotational engine speeds, and it is possible to fit friction material to a dynamometer for testing purposes, as well as testing brake capability on vehicles themselves.
Friction materials should be stable, with minimum fluctuations in their effectiveness. One of mica’s core qualities is its stability when exposed to temperature extremes and different environmental conditions.
There is also a need for general durability alongside low thermal conductivity, while not causing any damage to contact materials. Again, mica meets these criteria and performs reliably and consistently.
Other Environmental Considerations Of Brake And Anti-Friction Components
Along with the risks associated with asbestos as a friction material in the automotive industry, copper has an environmental impact too
Traditionally, due to its thermal stability, copper has been widely-used friction material. However, copper does not break down in the environment, which can then mean it accumulates in plants and animals.
Therefore, increasingly, the move is towards copper-free brake and anti-friction components.
Expert Solutions For The Automotive Industry
For more information about mica applications in the automotive industry, please phone us now on +44 20 8520 2248, email sales@elmelin.com, or complete our online enquiry form. We will be in touch with you as soon as possible.