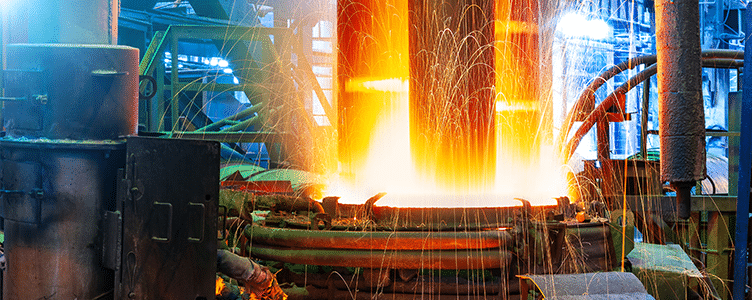
Industrial furnace safety – what you need to know
Working with incredibly high temperatures and potentially volatile materials on a daily basis means that considerations around industrial furnace safety are of critical importance.
While foundries and those operating a furnace will no doubt have their bases covered when it comes to protecting employees from the dangers of working with the furnace, there are additional considerations to be taken into account, and additional measures that could tighten up safety even more.
Let’s look at some of the safety risks in an industrial furnace and how these can be addressed with innovative insulation solutions.
The risks
At the very least, improper maintenance or insufficient lining on a furnace could result in damage to the lining. This can lead to increased maintenance costs and increased furnace downtime as you will be forced to replace the lining and possibly the coil grout more often. At the very worst, not having the right measures in place can cause damage to the induction coil – which can lead to explosion if the damage is serious enough.
This kind of damage could obviously prove costly in terms of the repair or replacement of equipment, but could also potentially be a very serious safety hazard to those working in the foundry.
Industrial furnace safety measures
There are a number of steps you can take in order to prevent damage to your furnace lining and potentially disastrous damage to the coil.
Slip-plane lining
A mica-based lining for your furnace can help to increase the life of your lining, as well as allow for expansion and contraction of the working lining to reduce the risk of damage from metal reaching the coil grout and beyond. This in turn means you have to replace the furnace lining less often, reducing maintenance costs and potentially costly downtime for your furnace. In addition, safety is increased through the protection of the furnace lining.
Early warning systems
It is not always possible to prevent metal from penetrating the furnace lining. Using the right material, you can put in place a dielectric barrier and sensor system which will act as an alert to you when the crucible is wearing thin and metal is penetrating close to the induction coil.
Elmelin’s Elmesh solution, a flexible laminate comprised of muscovite or phlogopite mica and a non-magnetic stainless steel mesh, was created and is optimised for this purpose. This will enable you to shut down the furnace and carry out necessary repairs before any damage is done.
Enhanced early warning systems
While solutions like Elmesh will help you increase safety by warning you when the metal has penetrated the crucible, additional measures can be put in place to enhance this and provide additional assurance, protection and savings on maintenance.
Elmelin’s Vapourshield solution is a stainless steel layer between two sheets of mica, which when connected to your earth leakage system can alert you when metal vapours penetrate the crucible and hits the Vapourshield layer. Depending on the temperature reached in the furnace, Vapourshield can also act as a barrier to metal penetration from the coil grout reaching the coil, again preventing potentially catastrophic damage.
Elmelin’s specialist solutions have been trusted by the foundry industry for decades. Get in touch to find out how we could help you improve the safety of your furnace while saving money on maintenance and repairs.