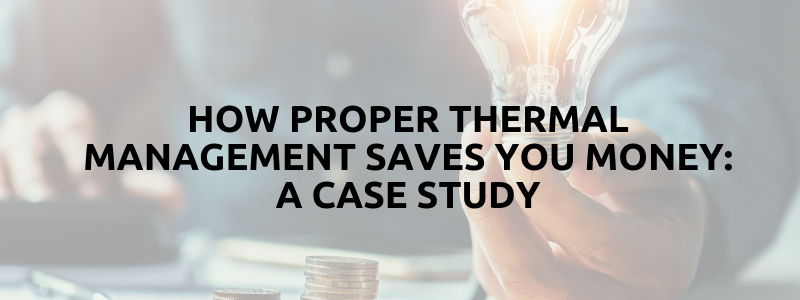
How Proper Thermal Management Saves You Money: A Case Study
With rotary kilns, thermal management is the key to improved productivity and reduced downtime, leading to savings in both energy consumption and the cost of repairs and maintenance.
Elmelin manufactures and supplies Elmtherm, a microporous heat insulation material for improved thermal management.
The following case study illustrates how proper thermal management using Elmtherm can save money for companies in the foundry and steel industry operating rotary kilns.
Annual Repairs, Downtime Costs and Operational Inconsistency
Rotary kilns must run at extremely high temperatures but must also control these temperatures in order to cause the necessary chemical reaction in the materials they are processing.
In aluminium processing, for example, this involves heating bauxite, the principal aluminium ore, which purifies the material.
Rotary kilns create a harsh processing environment, which means complications can arise both in maintaining optimum heat levels and in the operational effectiveness of the kiln itself.
In this case, the rotary calciner kilns have had to cope with frequently excessive shell temperatures, often above 380°C.
Consequently, the kiln was consuming large amounts of energy and required regular repairs.
For a rotary kiln to be effective in processing a chosen material, it must maintain the right temperature for carrying out the process of oxidisation, leaving only the valuable component in the material.
Therefore, sound thermal management is crucial to the success of rotary kilns in maintaining their technology readiness levels (TRL).
The Microporous Thermal Management Solution
As a material, microporous insulation achieves low thermal conductivity because it resists all forms of heat transfer, whether via gaseous conduction, solid conduction or radiation.
In insulation materials, there are gaps, or voids, containing air. The effectiveness of any such material depends on how much heat it conducts when molecules collide in these gaps, transferring energy from faster moving molecules to slower moving ones.
Microporous materials are based on separation technology. What this means is that they contain micro-pores of small, dispersed silica particles. These pores are so small that they leave voids that are too tiny to allow for collisions between molecules. The molecules cannot then interact with their neighbours, restricting the thermal conductivity of the air.
What this means is that Elmtherm, as a microporous, high temperature insulation material, offers a superior performance when it comes to thermal management in rotary kilns.
We have specially formulated this material to withstand extremely high temperatures without suffering any damage.
It addresses conductive and convective heat transfer and reduces heat transfer from radiation through incorporating infrared opacifiers.
The end result from applying Elmtherm is helping furnaces maximise their volume while reducing their energy costs and their downtime through furnace maintenance.
At the same time, Elmtherm’s advanced thermal stability means that it allows for much greater control of processing temperatures to help ensure consistency in rotary furnace operations.
Saving Money Through Sound Thermal Management
In this case study, before using Elmtherm to repair the kiln, the average temperatures of the surrounding shell were coming in at 283°C.
After the use of Elmtherm to repair the kiln, recorded temperatures for the entire kiln were averaging 237°C, a 46°C reduction in temperature.
In theory, this could save 20kg of fuel per ton of aluminium produced.
In terms of costs, the use of Elmtherm saved the client the equivalent of £8,800 per month, with an annual projection of £99,000 in total cost reduction.
This saving will go a long way to offsetting the cost of complete kiln repairs using Elmtherm.
A Legacy of Improved Performance
The client’s rotary calciner consists of three kilns. There have been year-on-year repair costs arising from maintaining all three. After initial repairs of the rotary kiln lining using Elmtherm, there will be further savings from repairing the remaining two kilns.
Applying this microporous technology can provide reductions in refractory shell temperatures across the board, including where there are variations in refractory thickness involved.
Not only this, but microporous insulation has significantly higher thermal conductivity than other forms of insulation, such as ceramic fibre blankets.
Generally, microporous insulation will result in a 20°C improvement in shell temperature reduction when compared with conventional insulation, preventing heat loss and driving greater efficiency in rotary kiln operations.
In this case study, the average shell temperature reading was 46°C lower after only an initial 13m repair of the shell. Therefore, a full repair of the total kiln lining using Elmtherm should offer a massive improvement in performance.
Future Applications of Elmtherm
Beyond kiln repair, Elmtherm offers microporous thermal management solutions in a number of applications. These include controlling transfer ladle temperature by applying an improved refractory layer. This then extends the ladle’s lifespan. It can also mean an increase in ladle capacity and therefore productivity.
Microporous material also works as a tundish back-up, and an insulation material for reheating and static heating equipment.
Contact Us for Thermal Management Solutions
We specialise in advanced high temperature and thermal management solutions, applying microporous technology to a range of products. Could your industry’s cost-effectiveness improve with the right kind of thermal management?
Please call us on +44 20 8520 2248, email sales@elmelin.com, or complete our online enquiry form. We’ll get back to you as soon as possible.