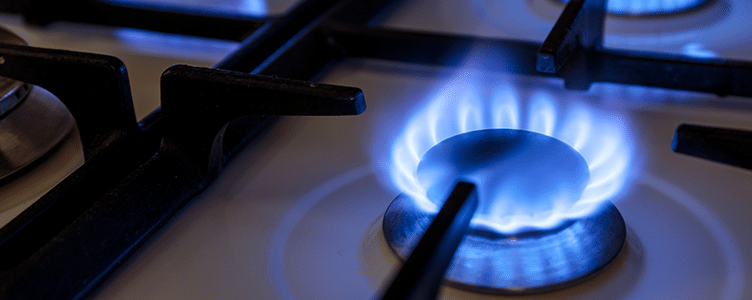
Heat dissipation and insulation: what you need to know
Heat dissipation is an unavoidable but nonetheless negative side effect of a number of processes in a range of industries – from forging steel to powering an electric vehicle. Heat dissipation and insulation both need to be considered for ensuring maximum safety.
A number of factors can affect heat transfer. It’s important to understand what these factors and outcomes are in order to find the right way to address the heat dissipation with the right insulation.
Here’s what you need to know about heat dissipation, and how thermal insulation can help address it.
Factors affecting heat transfer
The thermal conductivity, thickness and total area of the material impact how effectively it dissipates heat. There’s an equation for calculating the rate of heat transfer across the material, which is as follows:
Rate of heat transfer = k•A•(T1 – T2)/d
K = thermal conductivity value
A = surface area
T1 = temperature inside the object
T2 = temperature outside the object
d = thickness
Obviously, different materials have different levels of thermal conductivity. Metals, as good conductors of heat, have higher thermal conductivity values (measured in units of W/m/°C). Aluminium has a k value of 237, copper 398, gold 315. The application will also affect the rate of heat transfer. If we’re talking about a furnace or kiln, the inside temperature will likely be upwards of 1000°C – so without any type of insulation, you would expect the rate of heat transfer to be considerably higher.
Insulating materials, such as mica, have much lower thermal conductivity values. Mica has thermal conductivity of approximately 0.71 – meaning the rate of heat transfer through mica is much lower. Our Elmtherm microporous products have thermal transfer rates much lower at 0.020 W/mK at low temp and 0.036W/mK at higher temperatures.
Thus, through adding an insulative layer with a lower thermal conductivity and therefore a lower rate of heat transfer, you slow down the rate of heat transfer (or loss) overall.
This slowing down of heat transfer can be vital for a number of reasons.
Reducing costs
Loss of heat during manufacturing processes – especially those which require incredibly high temperatures – can have a big impact on the energy consumption and therefore the cost of running equipment. Taking an example from a recent project we worked on providing thermal insulation for rotary kiln – in a specific section of the kiln, prior to installing our Elmtherm solution, the rate of heat transfer was on average 182 mJ/H (mega-Joules per hour). Following the repair of the kiln using our solution, the rate of heat transfer was reduced to 109 mJ/H – a 40% reduction. This led to significant savings on energy consumption – saving around 15.1 kg/T of fuel in production, translating to an annual saving of £90k.
Safety
In industrial or even consumer settings, the reduction of the rate of heat transfer can be vital for making the equipment safe to use, often in order to comply with strict industry regulations. In a more specific example, reducing the rate of heat transfer can be especially important in electric vehicles. Electric vehicles (EV) are powered by lithium-ion batteries. These batteries are ideal for powering EVs because of their high energy density, but unfortunately they are at risk of a process called thermal runaway. Thermal runaway occurs when the battery short circuits or malfunctions – causing an increase in temperature within the cell, which quickly spreads to the rest of the pack via heat transfer. This creates an unstoppable chain reaction, incredibly high temperatures throughout the pack, and eventually, fire or explosion. Utilising insulation between the battery cells and in the housing of the pack enables you to slow down the rate of heat dissipation, giving the occupants of the vehicle more time to reach safety.
Reducing maintenance costs
Consistent exposure to extremely high temperatures negatively impacts a material’s thermal properties and even structural integrity. Without proper insulation, accelerated heat transfer could mean the system or machinery has to be repaired more often. This leads to increased downtime, loss of productivity and ultimately, higher costs.
Addressing heat dissipation with mica-based insulation
Using the right type of insulation, depending on your application, can help you significantly reduce the rate of heat transfer, reduce costs, and increase efficiency and safety. Elmelin have been designing and manufacturing bespoke, mica-based insulation solutions for over 100 years. We work with a wide spectrum of industries, including foundry and steel, electronics, automotive and continuous processing to help select the right type of insulation. If you’d like to find out more, get in touch.