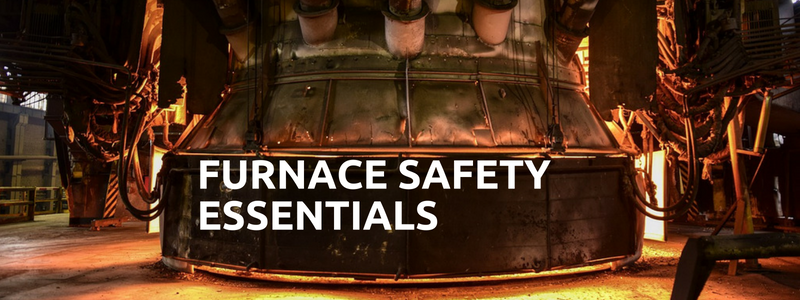
Furnace Safety Essentials
At the heart of the foundry is the furnace, and furnace safety essentials are at the core of how the foundry industry operates. Furnaces require high temperature insulation to work effectively, efficiently and safely. Foundries involve an inherent degree of risk, because furnace processes involve constant intense temperatures and the movement of molten metal.
At the same time, foundries are under pressure to improve productivity while keeping overheads down, or even reducing them, to compete in an industry which is continuing to evolve technologically.
Therefore, it is logical that furnace safety essentials include the adoption of technologically advanced materials alongside time-honoured methods and materials to both protect workers and ensure safety, while driving efficiency and improvements in production.
Here we look at how high temperature insulation solutions and furnace safety systems have become part of modern, forward-looking foundry industry practices, and Elmelin’s contribution to them.
High Temperature Insulation
Casting involves extreme heat and, importantly, the expert and precise control of this extreme heat. Without this control, the process will not produce the desired end product, and the risks are more acute for the people working in this environment.
The furnace must be charged with molten metal, which is then heated above its melting point. For the furnace to withstand these temperatures, and for it to help maintain them, to enable the casting process to take place, it must be properly lined and insulated.
Any loss of heat threatens the effectiveness of the process. It is vital, therefore, that furnaces have a suitable lining material, which is where mica comes in.
Mica’s unique mineral properties make it ideal for lining furnaces as it extends the life of the lining while offering the right degree of flexibility for when the lining expands and contracts.
This freedom of movement is essential to keep casting efficient and consistent. It also helps reduce downtime in foundries by reducing the frequency for when the furnace requires relining.
Microporous Insulation Technology
In addition to the excellent slip plane characteristics of mica laminates, furnace safety and efficiency also benefit from the application of advanced microporous insulation technology.
This comes in the form of lightweight sheets, at different grades, in our Elmtherm range. They are ideal in a range of furnace settings because of their space-saving adaptability.
Microporous insulation sheets work by combining a porous structure with low density, thereby reducing their heat conductivity. The sheets comprise small particles of silica which create micro-pores, which have tiny diameters of less than two nanometres. This structure means that the sheets create tiny air pockets which block the free flow of the air that would normally transmit heat through the material.
In action, Elmtherm sheets are effective in blocking conductive, convective and radiant heat, improving foundry processes and helping ensure furnace safety.
Providing thermal stability means furnaces can more easily control the extreme temperatures they work with, ensuring better consistency.
Pouring Molten Metal
A key risk area in the processing of molten metal is when this extremely hazardous material must be moved or transferred.
At the pouring stage, molten metal must be transferred from the furnace into moulds, often at temperatures exceeding 800°C. This usually involves a ladle or tundish.
Elmtherm provides a superior lining for ladles, giving them the added resilience to hold materials at temperatures of up to 1650°C, significantly increasing their capacity. Increasing ladle volume by 10% while improving on safety and energy efficiency, makes microporous technology a vital part of the casting process.
When it comes to tundishes, the use of Elmtherm helps extend operations, meaning foundries can commit to continuous casting while increasing the volume of what they process, due to the thinness of the microporous insulation material.
For furnaces, they combine this technology with established practices and processes, including their highly skilled employees wearing the appropriate protective clothing, and carrying out operations in designated areas, away from potential trip hazards.
Furnace Safety Applications
Alongside our high temperature insulation solutions, we help furnaces operate safely with safety systems designed to help prevent the risk of damage to furnaces during operations, and to reduce the risk of injury to workers in the foundry industry.
Our furnace safety systems include Elmesh, a mica mesh laminate that performs an essential sensor function; and Vapourshield, which functions to both prevent and warn against vapour penetrating the furnace’s coil grout.
Over time, crucibles can wear thin with use, increasing the possibility of damage to the coil grout during processing. Elmesh’s early warning capability gives operators the opportunity to shut down the furnace and take remedial action before any serious damage to the coil can occur.
The processing of certain metals carries with it risks of damage to the furnace itself. Galvanised scrap metal can emit fine oxide emissions during the smelting process. These emissions, if not observed or controlled, can lead to the build-up of deposits on the coil grout. These deposits may then eventually effect performance, causing faults or misreadings.
Vapourshield acts as a temporary barrier and an early warning system where there is a risk of this vapour penetration.
A Safe Working Environment
Foundries must ensure the safe working of furnaces and reduce the level of risk wherever possible. It is key that furnaces, ladles and other equipment is properly maintained, so that it is both safe and reliable.
High temperature insulation solutions and furnace safety systems contribute to the safe working environment that furnaces require, helping to prevent injury from molten metal, and damage to furnaces during the handling, movement and processing of molten metal at intensely hot temperatures. What our products also offer, is improved productivity and increased efficiency, alongside the protection of furnaces and the people working in them.
Are Maximising Your Furnace Operations?
Talk to us about your furnace requirements. We have a range of insulation and safety solutions which can help improve your productivity. Call us on +44 20 8520 2248, or email sales@elmelin.com. If you prefer, complete our online enquiry form and we’ll get back to you as soon as soon as we can.