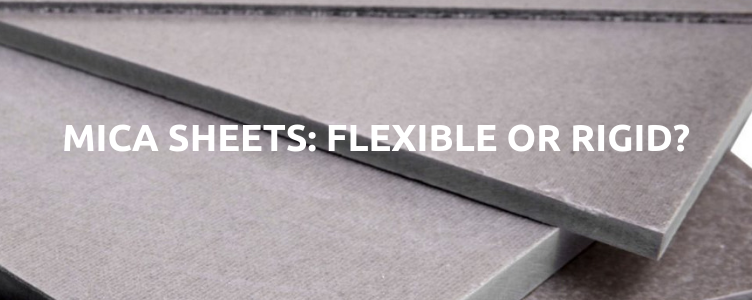
Mica Sheets: Flexible or Rigid?
Mica sheets come in flexible or rigid form and are suitable for various critical applications across a diverse range of industries.
Mica sheets come in flexible or rigid form and are suitable for various critical applications across a diverse range of industries.
Microporous high temperature insulation is based on microporous technology, which uses the separation of tiny particles as a highly effective form of thermal management.
…Cost effective industrial insulation is about more than saving money. It is about saving energy, reducing inefficiency, demonstrating clear environmental benefits and therefore helping boost industry reputations too.
…Reducing the UK’s carbon footprint is a business issue as much as a government one, as various industries depend on high temperature insulation for both their energy efficiency and profitability.
The UK Government is committed to reducing greenhouse gases to zero emissions by 2050. In fact, it is the first major economy to pass a zero-emissions law. It also has the concept of clean growth at the heart of its Industrial Strategy.
However, this then puts pressure on the industry to deliver the practical measures to reduce the country’s carbon footprint. One of the central aspects of achieving this will be high temperature industrial insulation.
The part high temperature industrial insulation plays in reducing our carbon footprint is a vital one, and it is all about cause and effect.
The key is energy efficiency. The more energy-efficient industries are the fewer emissions they cause, and the less energy they consume. High temperature insulation enables and supports this energy efficiency.
The more effective the insulation, the more energy-efficient the industrial processes or products. Consequently, it makes sense for businesses to invest in advanced high temperature insulation to, ultimately, reduce their carbon emissions.
What industries are we talking about here?
An obvious sector where insulation is central is in construction. However, many other industries depend on it to optimise performance and processes, including the foundry and steel industry, automotive, aerospace, power electronics and manufacturers of consumer appliances.
Elmelin’s role is to support these industries with specialist products that are designed to improve high temperature insulation and maximise energy efficiency in various industrial processes.
These products use mica and microporous technology.
While clearly industry is a major contributor of carbon emissions, how we live our daily lives also has a cumulative impact on the environment. This is why high temperature insulation in consumer appliances is critical in reducing our carbon footprint.
The more sophisticated and smart our consumer appliances get, the more energy efficient they will need to be. This is because their advanced electronics are both sensitive and heat-generating.
Within the manufacturing sector, mica provides high temperature insulation for a broad range of consumer appliances. These include hairdryers, toasters and microwaves.
Mica’s natural heat transfer properties and electrical resistance make it ideally suited for these types of product.
As technology advances, electronic devices and systems are becoming more energy efficient, but this depends on them having effective high temperature insulation to ensure their optimum performance.
At the intuitive, user-end of the process, simplicity combines with low energy use, but to achieve this requires an enormous amount of complex development, including minimising the heat transfer of powerful electronic components to enable them to remain stable.
As a material for capacitors, resistors and other components, mica provides a superior level of insulation and long-term durability for electronics in manufacturing.
Where once it might have almost been taken for granted that vehicles would continue to be a major pollutant and source of emissions, now the emphasis is very much on reducing the collective carbon footprint of the automotive industry.
The demand is for more efficient, cleaner transport, with the rise of the electric vehicle (EV) at the forefront of new developments in this sector.
The challenge it continually strives to meet is for enhanced performance while reducing its environmental impact. Again, electronic components in vehicles have become increasingly sophisticated and sensitive to enable these kinds of improvements.
For these components to function effectively and safely, they require the right degree of high temperature insulation. Mica laminates and components contribute significantly to vehicle efficiency and safety.
The latest generation of low and zero emission vehicles requires carefully managed battery temperatures. This temperature regulation, through insulation, is what enables them to reduce their environmental impact while maximising their output.
In this context, high temperature insulation is not about directly reducing the carbon footprint of electric vehicles, but ensuring that as alternatives they are operationally effective, and therefore an increasingly attractive alternative to consumers.
In the foundry and steel industry, there is an inherent amount of heat and energy in the processes used to melt different metals. High temperature industrial insulation extends the life of furnace linings, making them more energy efficient.
This is down to mica’s superior slip plane characteristics, which also help increase furnace capacity, supporting best practices when it comes to reducing the environmental impact of this industry.
Extending the lifecycle of products and improving the efficiency of industrial processes will help reduce the carbon footprint of industry as a whole, and of end users of manufactured products.
Elmelin’s high temperature insulation solutions apply to a broad spectrum of industries, and include practical R&D support for new or refined and adapted products and processes.
Can we help you reduce your carbon footprint using high temperature industrial insulation? Call us on +44 20 8520 2248, or email sales@elmelin.com. You can also complete our enquiry form and we’ll get back to you as soon as possible.
High temperature insulation in the foundry and steel industry is essential for preventing heat transfer during production of metal castings. Effective insulation also helps protect furnace linings, extending their lifespan and increasing their processing capacity.
…In the aerospace industry, thermal management materials are mission-critical. While safety and efficiency have always been at the heart of aerospace technology, the integration of more functions into smaller components now requires increasingly adaptable thermal management solutions.
…Thermal insulation is an essential process across a range of industries, but for many of its applications, there are also practical considerations to do with cost, as well as efficiency and adaptability. This is why thin thermal insulation is becoming a key area of research and development.
…A heat sink is a passive heat exchanger. This means it transfers heat from an object to a coolant, either air or liquid. This coolant then dispels any heat generated by the object.
Heat sinks are used in many essential electronic devices, including as central processing units in computers and in power electronics.
A good heat sink must be made of the right kind of material to perform its function well. Along with the material of the heat sink itself, another crucial aspect in its operational effectiveness is the thermal interface between it and the component.
Mica, with its natural conductive qualities, is an ideal material for use as a thermal interface and insulator of heat sinks.
Heat sinks must prevent overheating in electronic devices and components. To do this, they must be made of certain materials, which have a good degree of thermal conductivity.
Most devices using power electronics will require environments with controlled temperatures. Otherwise, they risk overheating, which can then affect performance or, more seriously, become a safety hazard.
Essentially, the heat sink acts as a pathway for any heat being generated to dissipate away from the device or component. This requires an optimum speed, to dissipate the heat from the source at the same rate as the source is generating it.
In fact, optimisation is the key to success of any heat sink system. This impacts on the choice of materials, along with essential aspects such as, complexity, size, mass and cost.
Therefore, while choice of materials is crucial, there are other factors to consider too.
The most common heat sink materials are aluminium and copper alloys.
Aluminium alloy provides the starting point for many heat sinks. This is because aluminium alloy has high thermal conductivity, but is also easy to manipulate mechanically because of its softness.
Another option is to bond copper and aluminium together, with aluminium remaining the dominant part, because of it lighter weight. This combination has been increasingly used in heat sinks for computers.
However, while aluminium surrounded by a copper plate can be effective, the copper and aluminium do not always bond together as tightly as necessary, making this cheaper option a less reliable one.
Another growth area is in carbon-derived materials, combined with aluminium. This takes advantage of aluminium’s lighter weight but is more conductive than copper.
Natural graphite composite materials are also on the rise in heat sinks. Again, the advantage here is weight.
Generally, in terms of performance, traditional aluminium and copper heat sinks perform most consistently.
The heat sink has fins in its design that provide the necessary surface area to dissipate the heat. The fins act to cool the source of the heat and the heat sink itself. Consequently, the efficiency of the fins is an important aspect of the heat sink’s performance.
Heat flows through the fin, the temperature decreases from its base to its end, from a combination of the heat sink’s thermal resistance, heat lost due to convection and the temperature of the fin.
The arrangements of fins in a heat sink also affects its performance. For example, heat sinks with pins that are either elliptical, cylindrical or square are fairly commonplace. Another type is a heat sink with a straight fin, running the entire length of the heat sink.
Colour can also be a consideration, since black surfaces with a matte finish radiate heat more efficiently than bare metal with a shiny surface.
The most effective heat sink for a specific function will combine good thermal management with suitable mechanical design, taking into account practical needs and cost effectiveness.
The heat losses from a power electronics device must get across different interfaces between materials. A component will have a casing, for example, so any heat must move from this to the surface of the heat sink. There is also the heat transfer which must occur between the heat sink and its surroundings.
Each of these transfers will have its own thermal resistance, and the combination of these will affect the efficiency of the entire system.
Therefore, the task of the relationship between device and heat sink, taking these things into account, is to minimise the overall thermal resistance or maximise heat flow.
The choice of materials acting as a thermal interface can help greatly in this function.
In computer processing units, for example, the thermal interface material will be positioned between the processor and the heat sink.
Used with other parts, mica components are an extremely effective thermal interface in heat sinks. These components include mica washers for use with heat conductive paste, and mica wafers for mounting semiconductors to heat sinks.
This is because mica is lightweight but strong, and highly adaptable. It is a technically superior insulator, able to withstand both intense electric fields and high temperatures.
As specialists in thermal management solutions, Elmelin can provide you with a range of mica-based products for heat transfer and insulation purposes.
Please phone us now on +44 20 8520 2248, email sales@elmelin.com, or complete our online enquiry form. We’ll get back to you as soon as possible.
Thermal management for electronics is critical where electronic components produce significant amounts of heat. Where this is the case, effective thermal management will prolong the working life of these components and also increase their reliability. Such components include power transistors, CPUs (central processing units) and power diodes used in the power electronics industry. For thermal management, mica offers adaptability and flexibility combined with high resistivity and stability. As an insulating material which will not conduct electricity, it is well suited in a wide range of applications in electronics.