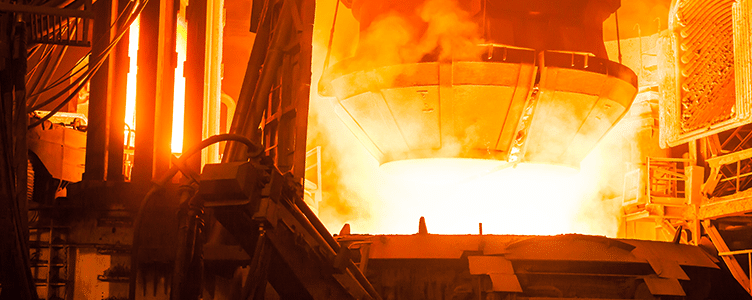
Thermal classifications for insulating materials
In our previous blog post, we examined in detail five thermal insulation materials and their physical and thermal properties. In this post, we’re going to get into official thermal classification of insulating materials, their importance when it comes to selecting the right type of insulation and the applications of the materials in each classification.
Thermal classification of insulating materials: How many classifications are there?
The thermal classifications for insulating materials are set by the International Electrotechnical Commission (IEC), specifically in their standard IEC 60085 – Electrical insulation – thermal evaluation and designation. In the USA, there are equivalent classifications used by NEMA (National Electrical Manufacturers Association), and in Japan, by the standard JIS 4003 C. We’ve covered the classes and their temperature thresholds on this blog before, but let’s just remind ourselves here.
IEC 60085 Class | NEMA Class | JIS C 4003 Class | Maximum hotspot operating temperature | Typical materials |
90 | 90 | Untreated paper, silk, cotton and natural rubber.
|
||
105 | A | A | 105 | Most commonly Class 90 materials (paper, silk, cotton) that have been impregnated, coated with or immersed in a dielectric liquid such as oil. |
120 | E | 120 | Plastics, resins and polymers such as polyethylene, polyurethane, and epoxy resins. | |
130 | B | B | 130 | Inorganic materials and combinations of materials such as mica, glass fibers and asbestos. |
155 | F | F | 155 | Consists of Class 130 materials combined with other materials capable of withstanding the higher temperature. |
180 | H | H | 180 | Class 130 materials with high temperature binders, as well as silicone elastomers (silicone rubber) |
200 | 200 | Teflon, and class 130 materials with high temperature binders capable of withstanding 200. |
Higher classes including 220, 240 and 250 were added to the standard in 2007. These simply refer to lower class materials with high temperature binders which increase the capability and maximum hotspot operating temperature of the material. After 250, classes increase in 25C increments.
What is maximum hotspot operating temperature?
The maximum hotspot operating temperature refers to the operating temperature of the machine in which the material is used as insulation. It is calculated by adding the rated ambient temperature of the machine or system, an allowance for operating temperature rise, and 10C hotspot allowance. If the hotspot operating temperature is reached, the insulation does not fail, but its useful operating life declines at an increased rate.
Class 90 and 105 applications
The use of materials like paperboard for electrical insulation dates back to the early-mid 20th century. In the late 1920s, manufacturers began impregnating pressboard with dielectric oil to improve its insulation capabilities. This was commonly used in a wide range of applications, including transformers. Papers, silks and cottons are also used in the manufacture of telephone cables, capacitors and transformer boards.
Class 120 applications
Plastics and polymers have the advantage of both an above average thermal performance, and being light and easy to shape. For that reason they are commonly used across a wide range of applications, including aerospace, automotive, electronics, domestic appliances, and more in components such as seals, washers, bearings and wire insulation. Ostensibly, it is advantageous where possible to use higher class materials to allow for higher temperatures in some applications.
Class 130 and above applications
Materials classified as 130 and above are useful in high voltage applications, because of their ability to withstand higher temperatures. This could include converters, transformers and other power electronics. Class 130 materials such as mica and ceramic are commonly used in the manufacture of capacitors and resistors.
Mica’s thermal capabilities
Mica falls into Class 130 and above – pure phlogopite mica can withstand temperatures of up to 1000C. In addition to having superior thermal capabilities, it can also withstand up to 2000V, and is an excellent dielectric. Mica is also easy to shape and cut into a variety of specifications.
If you have a high voltage or high temperature application, and would like to discuss the benefits and capabilities of mica, get in touch. Our experts will help you create a tailored solution that works for you.