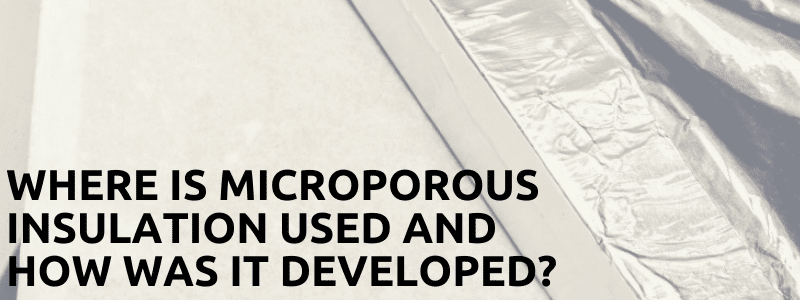
Where Is Microporous Insulation Used And How Was It Developed?
Elmelin specialises in an innovative range of microporous high-temperature insulation materials that are used in a wide range of applications – including aircraft, military vehicles, nuclear power plants and furnaces. These materials are designed to give superior performance in all conditions.
What Is Microporous Insulation?
The history of microporous insulation goes back around 70 years. This high-performance insulation material was developed in the 1940s by US military scientists, in the process of finding materials that would provide highly efficient thermal insulation for use in aircraft.
When creating this new insulation material, the US military defined the requirements as:
- Optimization of thermal performance without the use of a vacuum
- Service temperature use limit up to 1832°F (1000°C)
- Very lightweight
- High compressive strength
- Little or no out-gassing in service
Microporous insulation can be defined as a composite material that comes in the form of powder or fibre, with small particles of dispersed silica, creating micropores with diameters of less than 2nm (nanometres). This is similar to, or smaller than, the mean free path of air molecules at the standard atmospheric pressure.
Microporous high-temperature insulation is based on separation technology, which creates a mixture of materials and micro-pore structures. This provides thermal insulation with low density and low thermal conductivity, throughout a wide range of temperatures.
Microporous high-temperature insulation sheets block three modes of heat transfer: conduction, convection and radiation.
Reduced Conduction:
Due to the makeup of microporous insulation, contact between molecules is minimised meaning there is a reduced transfer between molecules, which reduces thermal conductivity.
Reduced Convection:
The microporous structure traps air pockets that are small than the free pathway of air, which would normally transmit heat meaning there is less convective heat transfer, this is because the material itself is made up of around 95% air.
Reduced Radiation:
Our microporous high-temperature insulation also incorporates infrared opacifiers. These opacifiers scatter a very high proportion of the infrared radiation, meaning there is a reduced amount of heat transfer from radiation.
From Nuclear Power Plant To Aerospace
Microporous high-temperature insulation is used in a vast number of different industries and is especially prevalent in high technology industries, being found in everything from nuclear power plants through to aerospace applications.
In the nuclear power industry, heat control within the nuclear steam supply system (NSSS) is essential. The NSSS consists of various elements including the reactor, pipes, pumps and valves and microporous insulation is used throughout the NSSS.
There is a large net positive heat load in a nuclear power plant and insulation is necessary to control containment cooling loads. If the heat is reduced at a greater rate than the cooling equipment can remove it, this can cause containment air temperatures to rise above safe levels, which is potentially devastating consequences.
In the aerospace industry, high performance microporous insulating products can be found in a wide range of applications including heat shields and protection for data recorder boxes.
It provides a fire-proof and heat resistant covering for interiors and exteriors without the need for a vacuum. It has high compressive strength, has little or no out-gassing in-service and being lightweight, it can offer high protection without affecting airborne performance.
Why Is Microporous Insulation So Effective?
At low temperatures, most insulation performs in a relatively comparative manner, however, microporous insulation performs optimally at higher temperatures. It’s also a cost-effective solution and can ensure the optimal efficiency of high-temperature technologies, such as furnaces.
What Can Microporous Insulation Do For You?
Our high-temperature microporous insulation Elmtherm enables you to increase your volume while offering considerable energy savings and reducing your carbon footprint.
It offers an impressive return on investment through its reduction of operating costs for furnaces. In addition, it’s quick and easy to install, due to its lightweight nature.
Besides saving on weight, space and energy, microporous insulation also has superb thermal stability, which means it enables better control of operating temperatures, bringing more consistent results.
- Elmtherm is used to line ladles, allowing them to hold molten metal up to intense temperatures of 1650°C, increasing their capacity, boosting furnace productivity while reducing production costs. Elmtherm can increase ladle volume by 10% and offer a 50% improvement in energy efficiency.
- For tundishes, Elmtherm enables extended operations and continuous casting, providing both refractory and backup insulation.
- It can reduce insulation thicknesses by 28mm while lowering heat loss by some 40%. At the same time, it increases usable volume in the tundish.
- In aluminium launder systems, Elmtherm optimises the movement of molten aluminium from smelter to casting, while minimising heat loss and reducing the need to superheat the metal.
- For melting furnaces, the use of Elmtherm as insulation helps ensure product quality through the even distribution of heat.
- It extends the furnace’s life and offers energy savings through a 30% heat loss reduction. When compared to fibreboard, its insulation is half the thickness, therefore increasing heating efficiency.
- Elmtherm is also used in kilns and rotary kilns, in tunnel and reheat furnaces.
A Case Study On ROI Using MPI
We were approached by a client with a kiln where the surrounding shell was operating at temperatures of 283°C. We advised the client to install our microporous insulation, Elmtherm. Following the repair of the kiln using Elmtherm, the kiln recorded temperatures of 46°C less than it had done previously.
We estimate this could save around 20kg of fuel per ton of aluminium produced, saving the client the equivalent of £8,800 per month with a projected saving of £99,000 per year. This goes a long way to offset the costs of kiln repairs using Elmtherm.
Contact Us To Start Benefiting From Microporous High-Temperature Insulation
We specialise in microporous high-temperature insulation products for use across a range of industries including the foundry and steel industry. Read more about our high-temperature insulation here or alternatively, please call us on +44 20 8520 2248, or email sales@elmelin.com or alternatively please complete our enquiry form.