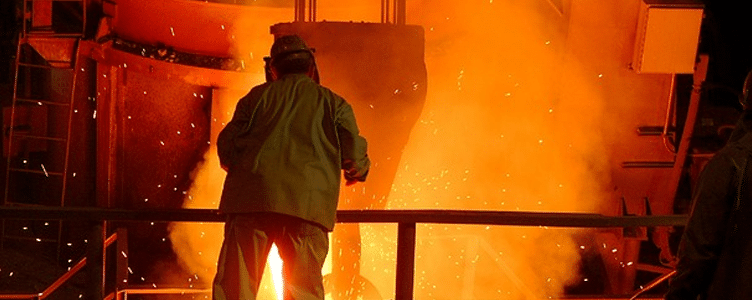
The advantages of using mica insulation in foundries
At the extreme operating temperatures in the foundry industry, it’s vital that the right insulation and the right insulation material be used to ensure an adequate level of safety, consistency and efficiency. We have been working closely with the foundry industry for many years – and as such have developed a number of highly effective mica-based insulation solutions that can help to increase safety, reduce maintenance costs and increase efficiency by significantly reducing heat loss.
Let’s explore some of the reasons why mica insulation is advantageous in a variety of applications in the foundry industry.
Slip plane material
Over the useful lifetime of a furnace, the ramming mass will sinter, causing it to become lodged tight against the coli grout. This can lead to costly maintenance, requiring the lining to be removed and the coil grout replaced, meaning extensive downtime. Many foundries now choose to line furnaces with mica slip plane – usually a laminate sheet or roll of pure mica, mica reinforced with glass or silicon resin, providing additional protection for the furnace lining. This is highly beneficial in a number of ways.
Extends the life of the furnace lining
When a furnace has a layer of mica or combi mica as a slip plane, the lining can move freely with expansion and contraction – which depending on the ramming mass can expand as much as 5%. The mica lining reduces the possibility of cracks forming in the lining through this continued movement, thus reducing the frequency of required maintenance.
Protecting the coil grout
Through allowing the lining to expand and contract more freely, the mica slip plane ensures less stress on and damage to the coil grout. In addition, when it comes to the furnace being relined, it separates the refractory from the coil grout, allowing the refractory and the slip plane to effectively slide out, protecting the coil grout and the rest of the furnace from damage.
Improved throughput and reduced downtime
As a result of reducing the need for maintenance and potentially costly and time-consuming repairs to the furnace and the lining, using mica slip plane allows you to increase the quantity of product which is melted for the useful life of each lining. Additionally, with the slip plane in place push out will be quicker, reducing the downtime needed to reline the furnace and as a result allowing more time for productivity.
Mica insulation improves furnace safety
Through the regular use of a coreless induction furnace, the crucible starts to wear thin, and there is a risk that the metal will penetrate close to the induction coil. If there is a breach in the furnace lining and the molten metal reaches the induction coil, this can lead to fire or even explosion. Failing to detect a breach in the furnace lining in a timely manner could have catastrophic consequences. Elmelin have developed a proprietary solution that provides and early warning system should there be a breach in the lining. Elmesh combines a layer of mica with a non-magnetic stainless steel mesh lining the furnace which can be connected to the earth leakage detector to give you and early warning that there is a breach in the lining and the metal may penetrate the coil. Vaporshield, another mica-based laminate solution, provides additional peace of mind and an extra early warning system for metal vapors such as zinc oxide leaving deposits on the core.
High temperature mica insulation
The final most common application of mica insulation in the foundry industry which offers significant advantages is high temperature insulation. Lining a furnace, ladle, tundish or kiln with high performance insulation helps to retain heat, maximise efficiency and demonstrate cost savings. Elmelin solutions use microporous insulation technology to improve performance and heat resistance, further reducing thermal transfer and improving heat retention and efficiency. Elmtherm is super lightweight, easy to install and shape, and therefore offers the additional benefit of reducing maintenance and relining times.
If you would like to learn more about how our specialised foundry insulation solutions benefit the industry, get in touch to speak to one of our experts. As well as specially designed off-the-shelf products, we can also work closely with you to design and develop bespoke solutions tailored to your exact requirements.