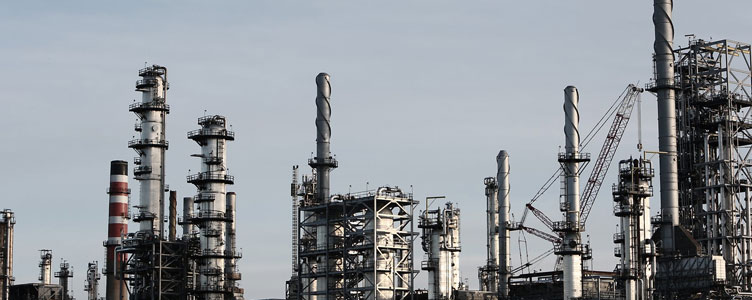
Reducing carbon emissions from heavy industry
Power and heavy industry sectors accounted for around 60% of annual emissions in 2019. Heavy industry describes sectors like steel, cement and petrochemical. The processes and fuels used in these sectors present significant and unique challenges when it comes to reducing emissions.
With the goal of net zero by 2050 fast-approaching, let’s take a look at some of the challenges of heavy industry and carbon emissions, and some of the ways they can be addressed.
The challenge
Heavy industry processes typically require extreme high temperatures, often upwards of 1000°C. Industrial heat makes up two-thirds of industrial energy demand, and one-fifth of global energy consumption. Currently, high temperature industrial heat relies largely on the burning of fossil fuels, which is a significant contributor of carbon emissions. To truly drive decarbonisation efforts in heavy industry sectors, there needs to be a significant shift in the way in which heat is generated.
Electricity can be used in some applications, but it can be impractical and expensive to reach extreme high temperatures of 1000°C or more. However, although electrification in itself helps those industries to reduce emissions, to truly contribute to the initiative the power sector itself must be made more sustainable, which we’ll look at in another blog post.
Renewable heat sources like solar and geothermal can be used for applications which require temperatures below 400°C, but can prove challenging to implement in many industrial facilities.
One of the more viable and exciting options is for industrial heat to be decarbonised through carbon capture, utilisation and storage (CCUS).
Carbon capture, utilisation and storage
CCUS comprises a range of technologies that can help to stop CO2 emissions from entering the atmosphere. It’s been found that capturing CO2 at key “point sources” – fossil fuel energy facilities, industries with significant emissions, etc – is the most effective way to extract it from the air.
There are currently around 20 commercially operational CCUS projects, and a further 30 have been agreed in the past three years. According to the IEA, CCUS projects could reduce global carbon emissions by as much as 70%.
Capture
For heavy industry, the most viable form of carbon capture is post-combustion capture – capturing the CO2 from a flue gas generated after burning a fossil fuel such as coal or natural gas. There are many technologies and methods being explored, but the most common are solvent-based, sorbent-based and membrane-based.
Solvent-based
Solvent-based CO2 capture chemically or physically absorbs CO2 from flue gas into a liquid carrier. The absorption liquid captures the flue gasses before they reach the chimney, and is regenerated either by heat or reducing press to break the CO2 bond.
Sorbent-based
This involves the capture of CO2 using a solid sorbent, which like solvents can be regenerated by increasing temperature or reducing pressure to release the captured CO2. Sorbent-based capture methods are less well developed and have heat transfer and stability challenges, but they can offer lower regeneration energies.
Membrane-based
This uses permeable or semipermeable materials that allow for the separation of CO2 from flue gas. This method can offer significant advantages over solvent and sorbent based methods as it doesn’t involve hazardous chemical storage and handling, and is more efficient at capture.
Storage
Once the CO2 has been separated from the flue gasses – it’s got to go somewhere to prevent it being released into our atmosphere. Various methods have been explored and developed for the permanent storage of CO2. Geological storage involves injecting carbon dioxide directly into underground geological formations such as oil fields, gas fields, saline formations and unmineable coal seams. CO2 can also be physically stored in containers with algae or bacteria which degrade it. Finally, mineral storage can also be utilised, where CO2 exothermically reacts with metal oxides, in turn producing stable carbonates.
Heavy industry and insulation
Elmelin work with manufacturers in many of the heavy industry disciplines, including foundry, steel, petrochemical and cement. We’ve developed a number of high temperature insulation and foundry safety solutions based around current processes and efficiency requirements.
As work continues to reduce carbon emissions from heavy industry, we’re working on our solutions to help them to face new challenges and bring in new processes. If you’d like to talk to us about a project, get in touch.