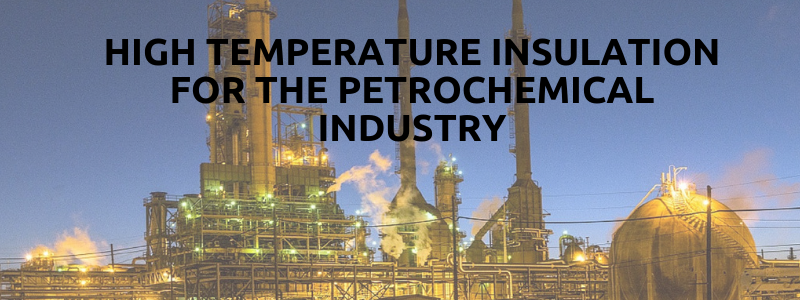
High Temperature Insulation for the Petrochemical Industry
In this blog, we will outline the growing need for high temperature insualtion in the petrochemical industry. The global market in high temperature insulation materials is growing. Statistics MRC has reported that it accounted for $3.6 billion in 2017, and predicting that this figure will reach $7.9 billion by 2026.
High temperature insulation is a critical aspect for many industries, including the petrochemical industry. At the same time the drive for greater energy efficiency and the rapid industrialisation of emerging economies are further boosting the need for insulation solutions.
There is a steady growth in demand for petrochemicals. Consequently, there’s a corresponding need for high temperature insulation to help ensure safety, energy efficiency and controlled or reduced emissions.
Key Features of High Temperature Insulation For The Petrochemical Industry
Insulation prevents heat transfer, protecting materials and elements close to a heat source, and reducing the amount of energy required to reach specified temperatures.
High temperature insulation materials must have a low thermal conductivity, to ensure a lower rate of heat transfer.
They require surface emissivity, to emit energy as thermal radiation.
And they need to have higher specific heat capacity, so that they take more time to absorb heat, before transferring it.
There are various high temperature insulation products, including calcium silicate and ceramic fibre.
Elmelin’s Elmtherm range is based on microporous technology and is used in a variety of applications and settings. This includes the petrochemical, cement and glass continuous process industries.
Lining Solutions for Petrochemical Processes
The petrochemical industry must meet increasingly stringent international standards and regulations designed to restrict and control emissions, pollution and environmental contamination.
The industry carries out certain processes that are integral to its operations which themselves carry hazardous risks.
These processes include:
- Crude oil separation – separating the different hydrocarbon compounds in crude oil into common, boiling point fractions such as liquified petroleum gas and residual heavy fuel oils
- Crude oil cracking – breaking large petroleum molecules down into smaller ones, converting heavier oil products into more in-demand lighter products, such as petrol and diesel
- Alkylation – combining small molecules into larger ones for components in petrol or diesel blending
- Isomerisation – rearranging the structure of petroleum molecules, which will produce higher-value molecules of a similar size as a more valuable petrol-blending component.
In these various processes, hazardous chemicals require handling and moving, through the use of process pipes.
Effective, high temperature insulation lining provides a superior level of protection for these means of transportation and containment. There are various materials which can do this, and a key one is microporous insulation.
It is highly flexible, durable and lightweight, with exceptional resistance to high temperatures.
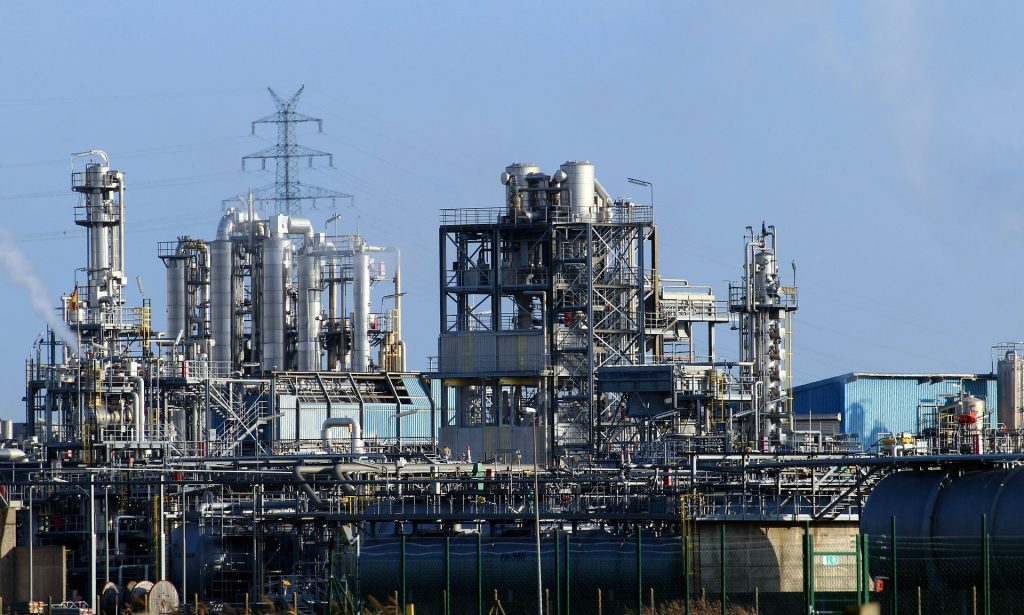
High Temperature Insulation for Direct Fired Heaters
Another aspect of processing in the petrochemical industry involves direct fired heaters.
These industrial heating systems heat crude oil to separators, as well as enable vaporisation of liquids and gases, and gas pipe heating.
Fired heaters reach significantly high temperatures, including the wall of the furnace itself. These heating operations are continual, which makes downtime a significant risk, and maintenance must be scheduled well in advance.
Therefore, the lining material for this equipment plays a crucial role.
It must have low thermal conductivity, superior resistance to thermal shock and an ability to withstand extremely hot temperatures.
The object of the lining is to protect the operations of the direct-fired heater and to extend its longevity while ensuring its reliability and consistency.
One material the petrochemical has relied on for this is refractory ceramic fibre (RCF), also known as aluminosilicate wool (ASW). However, while it performs well in harsh environments, it does produce by-products, which can be hazardous to workers.
These hazards are highlighted by the Health and Safety Executive (HSE), where it notes that the silicate fibres in RCF can irritate the skin, eyes and upper respiratory tract. The fibres are small enough to penetrate deep into the lungs, with the potential to lead to diseases such as mesothelioma or lung cancer.
Microporous technology provides a viable lining alternative that does not contain toxic fibres.
How Microporous Insulation Works
Microporous technology is a form of separation technology, using tiny particles for thermal management. The way these particles work means that they limit the three forms of heat transfer: conduction, convection and radiation.
Elmelin’s Elmtherm microporous insulation material consists of very small silica particles which restrict thermal pathways due to the restricted contact they have with each other.
This also restricts the movement of gas molecules, preventing them from transferring heat energy.
Elmtherm also addresses convection heat transfer by impeding the flow of air molecules within its structure. To restrict radiant heat transfer, it also includes opacifiers in its base components.
The result is a high temperature insulation product that can withstand temperatures of up to 1600°C.
Supporting the Petrochemical Industry
We specialise in high temperature insulation solutions to support continuous process industries. Here at Elmelin, we can provide high temperature insulation for the petrochemical industry.
For more information, please call us on +44 20 8520 2248, or email sales@elmelin.com. You can also complete our enquiry form and we’ll get back to you as soon as possible.