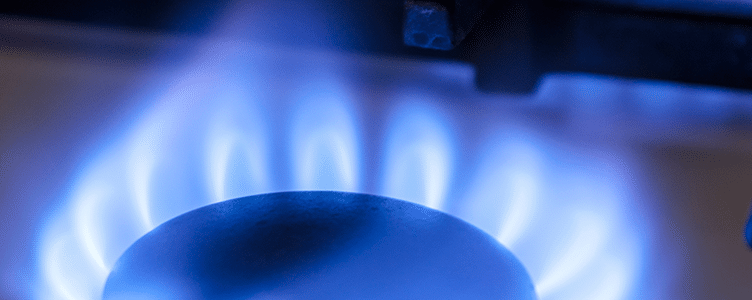
High temperature insulation: Comparing 5 common materials
High temperature insulation is vital in many manufacturing applications such as continuous processing, where operating temperatures should be controlled to achieve maximum efficiency and consistency, and foundry and steel, where effective thermal insulation can help to extend the life of equipment and provide additional safety measures.
In industries such as aerospace or military, the equipment is exposed to high temperatures due to external factors – be them intentional or accidental – meaning the right thermal insulation is required to ensure the safety of passengers and protect vital instruments.
For that reason, selecting the right type of thermal insulation is absolutely key. Here we’ll look at 5 common types of material used for industrial high temperature insulation, their properties, advantages and disadvantages.
Mineral wool
Mineral wool insulation is made from a mixture of glass, stone or slag which is heated to a high temperature and then spun into a light fibre structure. A common mineral wool product is Superwool, which is an alkaline earth silicate wool (AES). Mineral wools like Superwool are most commonly used in equipment that continuously operates, as well as domestic appliances.
Ceramic fibre
Ceramic fibre is produced by melting alumino-silicate materials in a furnace, from which a stream is poured and cooled to form fibre strands. It is incredibly lightweight, and highly resistant to thermal shock. Ceramic fibre is often used in furnace linings, pipe insulation, expansion joints, seals, fire protection, kiln linings, and packing for high temperatures.
Firebrick
Firebricks are blocks of refractory ceramic material, made from fireclay – a mineral aggregate composed of hydrous silicate of aluminium. They can withstand high temperatures and can help to ensure greater energy efficiency. Although they have superior thermal properties, one of their main disadvantages is that they are bigger, bulkier and heavier than other materials. Firebricks are most commonly used in the processing of metals, petrochemicals and ceramics. They are also used in kilns, fireplaces, furnace, forging furnaces, blast furnaces and flues.
Microporous
Microporous technology uses the separation of tiny particles as a highly effective form of thermal management. Microporous insulation was first developed for space and aerospace applications to be lightweight and therefore have exceptionally low thermal conductivity. The materials are made using small particles of products like silica – because of the restricted contact the particles have with each other, thermal pathways are limited, leading to superior thermal resistance and extremely low thermal conductivity. They also impede gaseous conduction and restrict convection and radiation, making microporous materials highly versatile for insulation. They are used in a wide range of applications including furnace lining, aerospace and process piping insulation.
Mica
Mica is a naturally occurring mineral with superior thermal and electrical properties. It forms in very thin sheets, meaning it is incredibly flexible and can be cut, stamped and shaped into a variety of forms. Pure phlogopite mica can withstand temperatures of up to 1000C. Mica is often composited with other materials like mineral wool, glass or ceramic fibres to enhance its thermal and physical properties. Mica composite laminates are available in sheet, roll or tube form, with sheet and roll being the most common in applications such as furnaces.
High temperature insulation comparison table
Material | Temperature rating | Thermal Conductivity (W/m.k) | Advantages | Disadvantages |
Mineral wool | 649C | 0.032-0.044 | Very low thermal conductivity
Low shrinkage Good strength Thermally stable Non-hazardous Cost-effective |
Compresses and sags with age
Absorbs moisture which reduces effectiveness. Loose effectiveness in forced convection situations
|
Ceramic fibre | 1260-1400C | 0.12 | Lightweight
Low thermal conductivity High thermal shock resistance |
Not abrasion impact resistant
Loose effectiveness in forced convection situations
|
Fire brick | Around 1649C | 0.15-0.56 | Good strength at ambient and elevated temperatures
Effective across a wide temperature range Low levels of impurity Low reheat shrinkage |
Heavier and bulkier than other materials
Not soundproof Low thermal shock resistance More porous bricks are weaker Not flexible in application |
Microporous (silica-based) | 1600C | 0.021-0.034 | Superior thermal performance
Long-term durability High compression resistance Low thermal conductivity and heat storage |
Can be considered dusty in certain applications.
Absorbs moisture and this reduces effectiveness. |
Mica (phlogopite) | 1000C | 0.71 | Flexible
Durable Non-hazardous Doesn’t absorb moisture Non-combustible |
Best used in combination with other insulation to enhance properties.
Can be heavy if used very thick |
Ultimately, selecting the right thermal insulation depends on your application and your requirements. We specialise in producing mica-based insulation solutions that are capable of handling a wide variety of high-temperature environments, including our mica-based insulation, Elmelec, and our microporous high-performance thermal insulation solution Elmtherm. If you would like to discuss your requirements with one of our experts, get in touch.