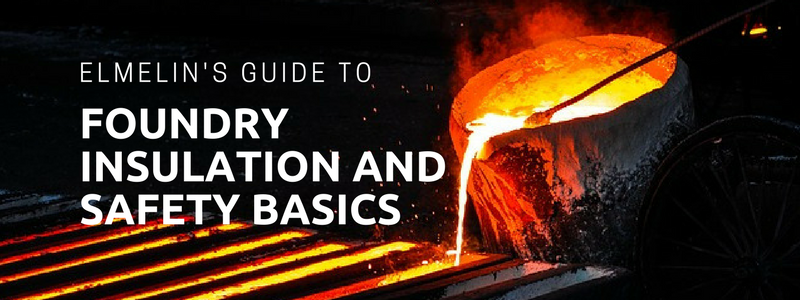
Foundry Insulation and Safety Basics
Foundry insulation is vital when it comes to foundry safety basics. Foundries work with extreme heat, using intense temperatures to melt metal and pour it into moulds. Due to the acute and constant levels of heat that they involve, these processes, therefore, carry a large amount of risk.
Foundries are inherently hazardous places. They will typically reach temperatures over 1425°C. If, for example, water encounters any active surface at these kind of high temperatures, it instantly expands to 1,600 times its original volume. Dampness is the enemy in furnaces, because even slightly damp metal can result in a massive explosion of intensely hot steam, with potentially catastrophic results.
Foundries require heat without moisture, which also means they create potentially hazardous conditions for starting fires. Uncontrolled fires are a risk, especially as foundries cannot rely on using water to put them out, due to the reasons mentioned above.
The solution lies in using flame retardant materials, in ensuring the best possible insulation of foundries, and in developing and ensuring safe working procedures constantly.
As specialists in foundry safety and insulation and in foundry furnace systems, we help and support the foundry and steel industry to continue to work safely and efficiently.
Mica in Foundry Design
With a basic requirement for thermal insulation and flame retardant materials, foundry design requires the right materials as a foundation. Rigid mica sheets provide ideal thermal insulation boards when manufacturing foundries, and apart from its vital application as a foundry lining, mica is also the basis for various components and process equipment.
Mica has natural mineral qualities of high temperature resistance and low thermal conductivity, along with high mechanical resistance and versatile machinability. Therefore, it is adaptable while being highly functional.
Foundry floors must be designed to minimise damage, particularly regarding spillages of molten metal. Consequently, rigid mica sheet’s non-reactive, flame-retardant qualities make it ideally suited for this purpose.
While safety is always a concern, many foundries now have newer generations of furnaces that are larger, safer and more efficient.
Foundry Insulation Solutions
The casting process involves charging a furnace with metal, and then heating it above the metal’s melting point. Charging is a very dangerous operation, requiring care and consistency in maintaining intense but constant temperatures. Insulation will prevent heat loss, but at the same time, it is vital that the furnace, and anyone working with, or near, it, is protected.
Mica-based insulation materials support the foundry’s combination of expert processing and precise thermal management, by extending the lifespan of furnace linings. Mica’s slip pane characteristics help allow the lining freer movement to expand and contract with a much reduced likelihood of cracks appearing.
Mica laminates also function to help protect the coil grout and the furnace casting.
There are also benefits in terms of efficiency, with mica foundry insulation increasing relining speeds and throughput, while reducing the potential for maintenance downtime.
Elmelin’s range of mica laminates and mica roll means we can offer insulation solutions across the foundry industry, from robust, glass-reinforced mica suitable for larger furnaces, to combi laminates for furnaces specialising in smelting aluminium and iron.
Early Warning for Coil Damage
Furnaces can be vulnerable to damage and breakdown, with serious implications for a foundry’s performance. The key is to detect the signs of damage, or a potential threat to the furnace’s stability, and catch it before it escalates with more serious consequences.
While furnaces which have integral crucibles usually have earth leakage detectors, we can enhance this by providing an early warning system of potential induction coil damage.
Elmesh is a flexible, mica-based mesh material. It is made from combining a phlogopite mica layer with another layer of non-magnetic, stainless steel mesh. This material acts as an early warning when there is a risk of metal penetrating the coil grout – something which can happen over time, as the crucible starts to wear thin with use. Foundries processing a diverse range of complex materials, such as scrap metal, are more likely to come across this issue.
This kind of early warning means operators can shut the foundry down before any impairment, and then take the necessary action to prevent serious damage to the coil happening in future.
This flexible solution comes conveniently packed in rolls, available in various grades of thickness and roll widths.
Preventing Vapour Deposits
Another foundry safety basic is preventing vapour deposits collecting on the coil. Where furnaces are processing large quantities of scrap metal that is galvanised, they run the risk of the material giving off fine oxide dust emissions during melting. Over time, these deposits can affect the coil’s performance, causing short-circuits or misreading.
Zinc oxide can also affect the quality of the smelted metal, with large cavities forming in it as result of gas build-up.
The Vapourshield mica laminate range works to both protect the coil from these deposits, and give an early warning where metal is close to penetrating the coil or coil grout during processing.
Vapourshield acts as a temporary barrier, but a timely one: scrap metals with high levels of impurity can cause the shut-down of furnaces, and mean foundries having the expense of replacing coils more frequently.
Prevention, Protection and Productivity
Like plenty of other businesses, foundries are looking to reduce their overheads while maximising their productivity. However, unlike many other businesses, they have inherent risks and hazards to contend with, in an industry where safety must come first.
Our foundry insulation products address several issues at once: they help prevent damage to furnaces occurring during essential processes; they act to bolster foundry safety by protecting both furnaces and those working in this environment with thermal barriers and optimised insulation; and they help boost productivity by making foundry processes more efficient.
Mica-based laminates and microporous insulation solutions are essential to the future development of the foundry and steel industry, and to its ongoing viability as a dynamic economic sector.
Do You Require Foundry Insulation?
We have a range of insulation and furnace protection products, and we can provide combined solutions bespoke to your specific needs. Please call us on +44 20 8520 2248, or email sales@elmelin.com. You can also complete our enquiry form and we’ll get back to you as soon as possible.