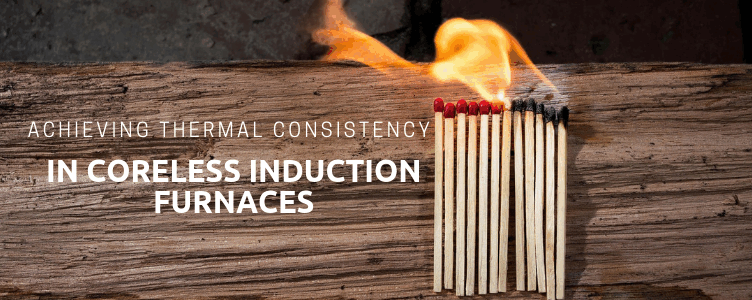
Achieving Thermal Consistency in Coreless Induction Furnaces
In the foundry and steel industry, production has been based on the principle of induction since the early years of the 20th century. Allen Colby patented the first induction furnace in 1900, and the induction heating of metal has spread since then, with most modern furnaces now using this electrical process.
The coreless induction furnace uses a crucible, into which metal is placed. A coil surrounds the crucible, which generates the electricity required to melt the metal in it.
For modern foundries using coreless induction furnaces to work efficiently, they must keep thermal consistency throughout this process. Maintaining the optimum temperature for the task will prevents the loss of valuable alloying elements, helping to achieve uncontaminated, well-mixed results every time.
Elmelin is a specialist manufacturer of products designed to support coreless induction furnaces in achieving this thermal consistency.
…