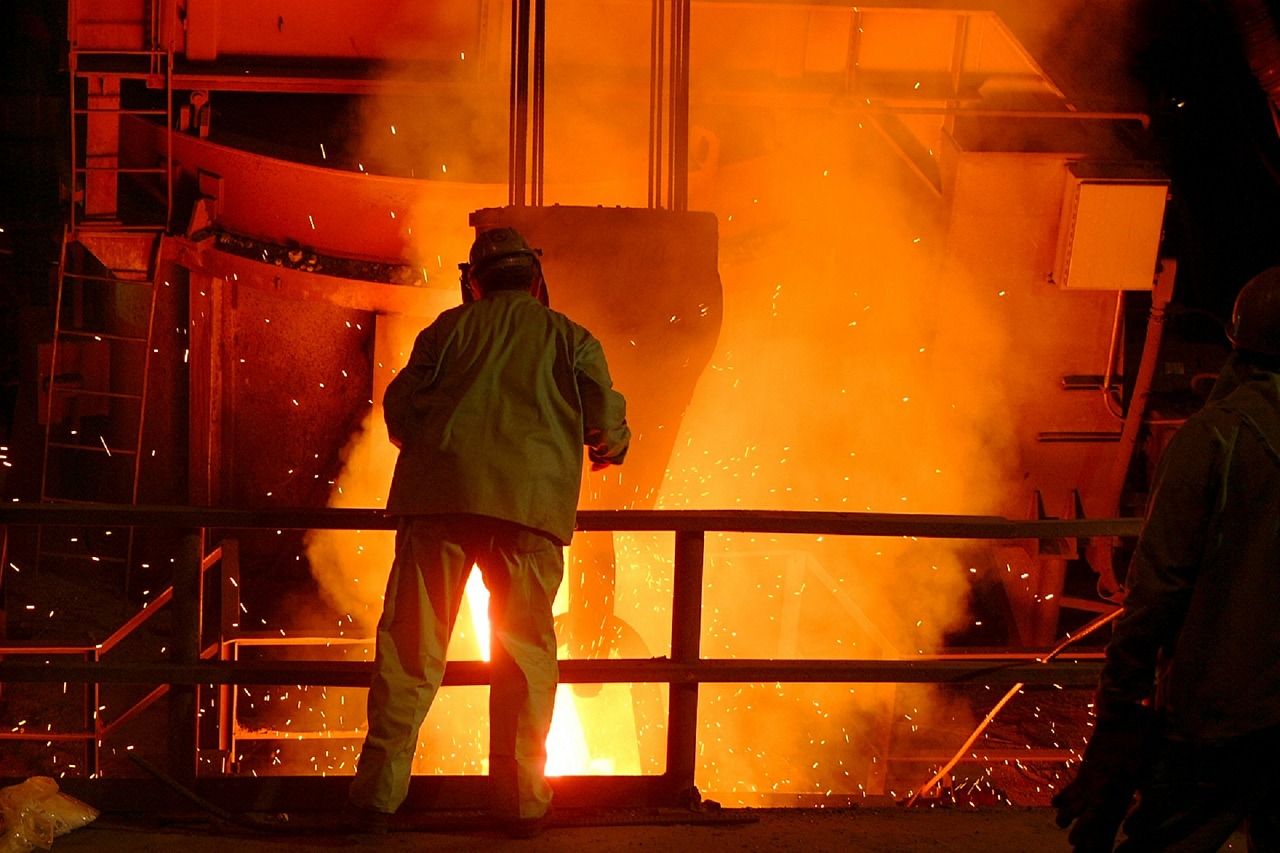
High Temperature Insulation for the Foundry and Steel Industry
High temperature insulation in the foundry and steel industry is essential for preventing heat transfer during production of metal castings. Effective insulation also helps protect furnace linings, extending their lifespan and increasing their processing capacity.
For the foundry and steel industry, Elmelin specialises in two key areas: high temperature insulation and furnace safety systems.
High Temperature Insulation Requirements
Not only do furnaces require intense heat for metal castings, they must also control this heat.
Charging the furnace with molten metal, then heating the metal beyond melting point requires proper lining and insulation of the furnace itself. If there is any loss of heat, through heat transfer, then this is likely to adversely affect the outcome of the process.
High temperature insulation helps reduce energy consumption, prevent heat loss and protect adjacent materials from heat damage. It also supports thermal consistency throughout furnace processes.
In coreless induction furnaces, for example, this thermal consistency prevents the loss of valuable alloying materials, which then assures that the resulting products are uncontaminated and of a sufficiently high standard.
Higher energy efficiency also means lower operating costs, along with assured quality.
The Use of Mica in High Temperature Insulation
Mica is a naturally occurring mineral that is extremely resilient when exposed to high temperatures, light, moisture and electricity. This makes it ideally suited to a broad range of applications and industries, including the foundry and steel industry.
Rigid mica sheets are used for insulating floors and wall areas of foundries. Flexible mica laminates are used to line furnaces, ladles and tundishes.
These laminates provide a thin but highly tear-resistant lining with superior slip plane characteristics. These characteristics greatly assist the efficiency of the melting process.
Mica laminates allow the furnace lining to expand and contract during melting processes, while protecting it from damage. They can withstand temperatures up to 1200°C. The more effective the lining material, the better the insulation and thermal management of the furnace.
Using a good furnace lining material also reduces downtime due to furnace relining, therefore helping to boost productivity.
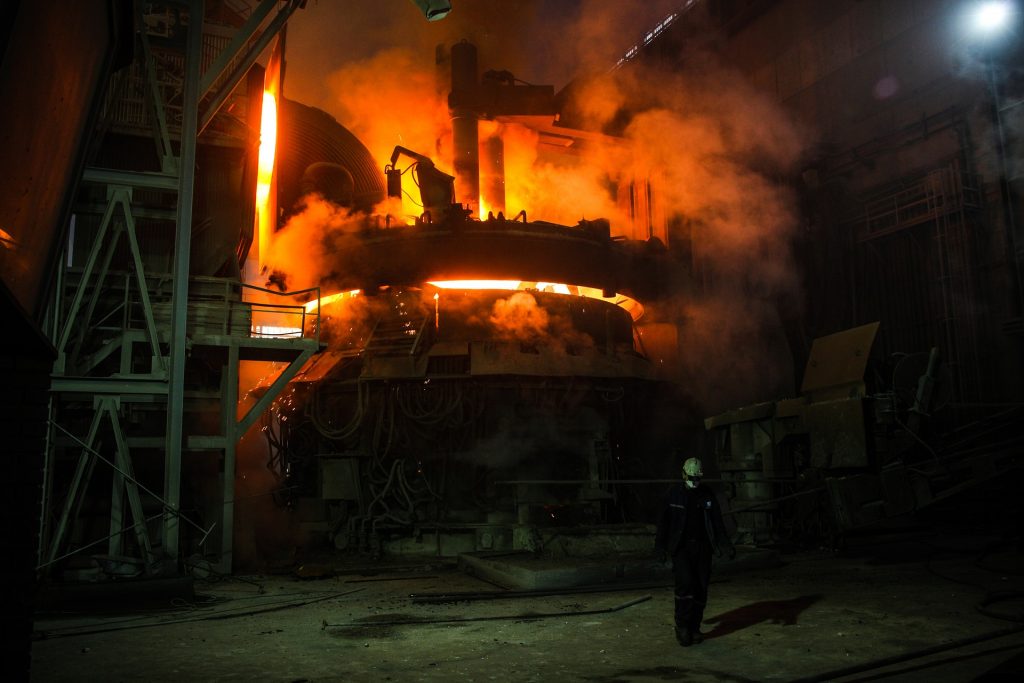
Flexible mica roll laminates come in various grades, including pure mica and glass-reinforced mica, either single or double-sided. For added strength, there is also a grade reinforced with scrim glass, especially suitable for larger furnaces.
Microporous Insulation Solutions
Microporous heat insulation uses micro-pores to minimise thermal heat transfer. These Elmtherm sheets save on space, weight and energy consumption. They are used to line ladles, which can then hold molten metal at temperatures of up to 1650°C.
Elmtherm can increase ladle volume by 10%, while offering a 50% improvement in energy efficiency. By reducing insulation thicknesses by 28mm in tundishes, Elmtherm increases volume but lowers heat loss during processes.
Applied to aluminium launder furnaces, this microporous high temperature insulation optimises movement from smelter to casting, and reduces the time required for heating the metal.
Insulation and Furnace Protection
During the melting process, there can be a risk of damage to the grout which protects the furnace coil, and to the coil itself.
In coreless induction furnaces, certain metals may cause contamination during melting by leaving deposits on the crucible lining, or on the coil. If the charge that goes into the furnace contains any traces of rust, sand, oil or grease, then these can cause damage and affect the integrity of the end product.
Scrap metal and some specialist alloys are also more likely to leave deposits.
The grout surrounding the coil is made of cement, which, overt time, will deteriorate with use. The danger then, where the grout is weakened, is that some of these deposits may penetrate it, and cause damage to the coil.
If vapour deposits do settle on the coil, this can cause misreadings or short-circuits. Another consequence can be thermal shock, where the furnace heats up or cools down its lining beyond the limits of its tolerance.
There can be a heightened risk of explosion in the furnace should thermal shock occur.
To protect and insulate furnaces, and provide an early warning of damage to the coil, Elmelin provides furnace protection materials.
Elmesh and Vapourshield
Elmesh is a flexible mica laminate combined with a layer of stainless steel mesh. In this form, it acts as a sensor, if there is any damage to the furnace lining.
Vapourshield is another mica-based laminate, designed to detect any traces of vapour emitted during the melting process, where materials such as scrap metal, copper alloys galvanised metal are involved.
Both these products provide high temperature insulation for furnaces with the added value of integrated furnace safety systems.
Ensuring Furnace Efficiency and Safety
Heat and its management are central to the foundry and steel industry. Elmelin provides specialist and fundamental support to this industry through a range of high temperature insulation, thermal management and furnace safety materials.
To find out how we can support your processes, please call us on +44 20 8520 2248, or email sales@elmelin.com. You can also complete our enquiry form and we’ll get back to you as soon as possible.