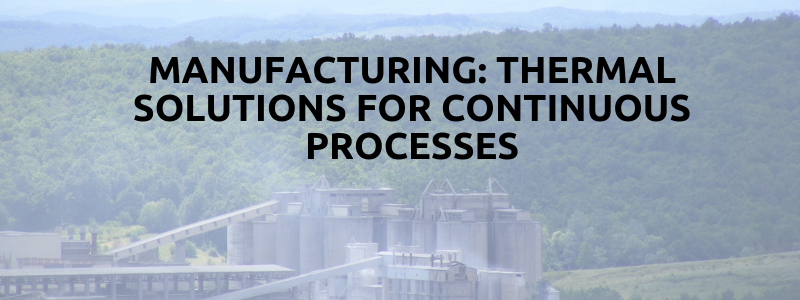
Manufacturing: Thermal Solutions for Continuous Processes
Cement and glass manufacturing are continuous process industries that require advanced and thermal solutions to optimise their output. Both manufacturing sectors depend on heat for processing. This means they depend on controlling this heat to ensure consistency and quality in their end-products. Thermal solutions for continuous processes centre on furnace lining materials. These include mica and microporous insulation.
In this blog, we’re going to look at cement and glass processes and outline how these high-temperature insulation materials support them.
Uses and Properties of Cement
Cement binds other building materials together, and it is used when producing mortar and concrete for construction. Cement is a commonly used material because of its good binding qualities. It provides strength when mixed with other materials.
Because of these qualities, cement plays a pivotal role in civil engineering projects, with a broad range of uses, including:
- in joints in pipes and drains
- for concrete for floors, construction lintels, roofs, beams, pillars and stairs
- in engineering structures, such as bridges and tunnels
- for preparation of foundations
- in the construction of roads, lampposts and water tanks
Cement is versatile, and its versatility depends on its properties. Consequently, the finished quality of the cement is hugely important.
Cement should harden or stiffen easily and provide strength to masonry. It should have a good degree of plasticity to make it easily workable. It must also be moisture-resistant.
The manufacturing process will largely determine the cement’s quality and in this process, thermal management is critical.
The most commonly used cement in general use is Portland Cement.
How Cement is Prepared
Cement manufacturing begins with raw materials extracted from quarries, which contain essential minerals. These include limestone, containing calcium; sand and clay, containing silicon, aluminium and iron. Other materials used in cement include shale, bauxite, mill scale and fly ash.
Once these raw materials have been transported, they will then be crushed into small chunks.
Cement composition depends on the proportions of these raw materials. Generally, cement is around 80% limestone and 20% clay. First, the crushed materials are milled into a powder, then mixed together. The mixing of these materials is known as prehomogenisation.
The next stage is to pre-heat this raw material mixture in a special chamber, drawing on hot gases produced from the kiln. This pre-heating stage helps reduce energy consumption in the kiln phase of processing. This helps to make it more environmentally friendly.
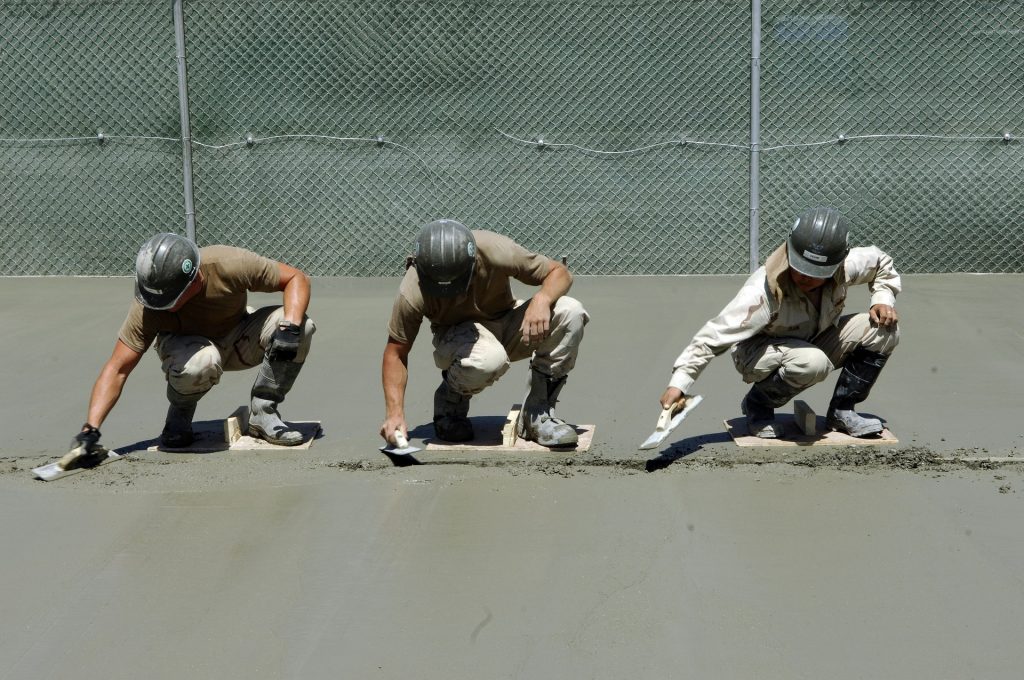
Calcination in a Rotary Kiln
The next part of the process involves high levels of heat. The mixture of raw materials is transformed into clinker, the material which will produce the finished cement powder.
Rotary kilns process material in a rotating drum for specified periods of time. The kiln is fixed at an angle to help the material move through the drum.
For cement production, temperatures reach 1400°C. The process is known as calcination. During calcination, the calcium carbonate in limestone decomposes into calcium oxide and carbon dioxide.
This is a complex process. It also requires evaporation of water and volatile constituents, and various chemical reactions. These stages happen in the kiln, based on temperature changes.
Temperature control is therefore critical to the success of the process. Thermal solutions provide the essential protection kilns require to withstand intense temperatures and to help regulate these temperatures as part of the cement manufacturing process.
Specialist microporous insulation products act as thermal barriers and reinforcement for cement kiln refractory linings.
Kiln efficiency is crucial to cement manufacture, and thermal insulation products aid in reducing downtime, emissions and energy consumption.
The main function of this thermal insulation is as a refractory lining, but it also plays a key part in other applications of the cement manufacturing process, including insulation in heat shaft exchangers, used in the essential precalcination process of cement production.
Thermal Solutions for Glass Processing
As a continuous process industry, glass production also depends on specific thermal solutions.
Like cement, glass is a versatile material with a broad range of uses; and also like cement, heat and thermal management are central to its manufacture.
Glass processing furnaces typically run at temperatures of 1500°C, on a continual basis. Therefore, over time, the molten glass will erode the refractory surface of the furnace, and may mean there is a risk of breach of the refractory wall.
These furnaces will have limited lifespans due to the sheer amount of work they process. However, the right furnace lining will help prolong their operational effectiveness, ensure the quality of output, and reduce maintenance downtime.
Mica laminates provide an ideal lining solution for glass furnaces. They are a highly durable combination of mica and a reinforcing glass fibre material.
Microporous Linings for Glass Kilns
Just as rotary kilns in cement manufacturing require sufficient protection and thermal management, glass kilns can also benefit from the use of lining materials that use microporous technology.
The separation technology underpinning these materials makes them well-suited for use in continuous process industries. Their porous quality ensures that they can reduce heat transfer and help kilns maintain optimum processing temperatures.
Expert Thermal Solutions for Continuous Processes
Here at Elmelin, we specialise in high temperature insulation and other thermal solutions for a range of continuous process industries. These include glass and cement production and petrochemical processing.
These solutions include mica-based laminates and our Elmtherm range of microporous insulation products.
For more information, please phone us on +44 20 8520 2248, email sales@elmelin.com, or complete our online enquiry form. We will be in touch with you as soon as possible.