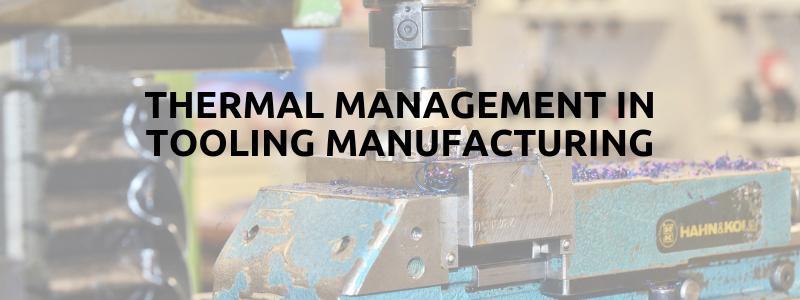
Thermal Management in Tooling Manufacturing
Tooling operations require precision, but at the same time, they generate heat, which is why thermal management in tooling manufacturing is critical.
Mica is an ideal material for thermal management in tooling manufacturing because it has excellent insulation properties, while also being extremely durable, adaptable and lightweight.
Here, we look at the issue of thermal management and controlling heat generated by machine tooling.
The Risk of Overheating in Tooling
Rising heat and humidity levels can be an issue for workers in machine shops, but they also have the potential to damage equipment too, with costly consequences.
The main risk is to the electrical components in tooling equipment, where overheating can cause moisture, which then results in corrosion. This can affect the performance of the equipment and cause faults, leading to costly downtime and maintenance.
There are ways to combat overheating. One is to monitor carefully heat and humidity levels in the working environment. Another is to have machines with internal quality assurance detectors.
However, another key means of protection from overheating is via thermal management.
Why is Thermal Management Important?
Thermal management is the means of controlling heat transfer using technology. A thermal management system will have a specific area of focus, depending on its application.
Cutting tool applications will generate heat, and thermal deviations in machine tools are therefore a major factor in errors and in maintenance. Controlling heat is crucial in prolonging the tool’s life and also ensuring its accuracy.
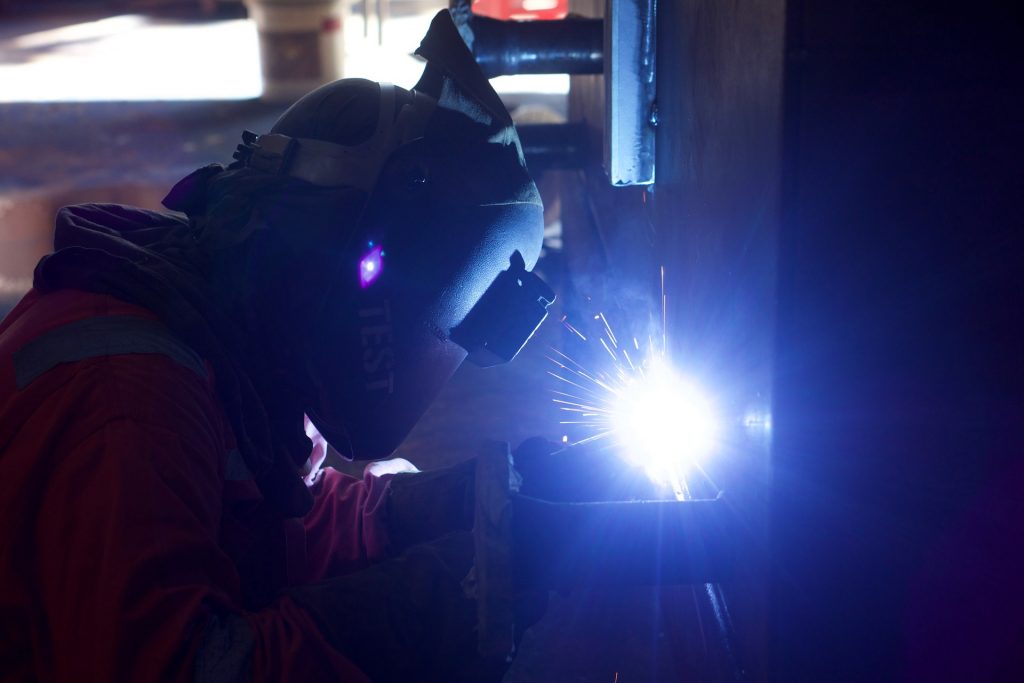
Heat can cause thermal drifts in machine spindle systems, causing deviations in cutting. Heat can also cause displacement where single tool elements expand or become deformed due to temperature changes.
There are various sources of thermal influences on machine tools:
- The cutting process and the heat it generates
- Heat from different heat sources within the machinery
- The thermal influence of heating or cooling systems
- Environmental conditions
- How people operate them.
The main heat source in most tooling applications will be the spindle system, including its motor and bearings. The bearings will have to carry the enormous load generated by the rotation speed of the equipment.
Other components can also generate heat, including electrical systems.
Thermal management in tooling manufacturing requires a focus on three key areas:
- Use of material in tooling applications
- Control of heat transfer
- Compensation for any deformation of parts resulting from temperature changes.
The Use of Mica for Thermal Management in Tooling
Much can be done at the design stage of machine tooling to help control heat transfer and minimise the potentially damaging effects of thermal influence on cutting processes.
The aim should be to design and manufacture machine tools for the best possible thermal stability.
As a manufacturing material, mica has insulating qualities and enables good thermal management.
Furthermore, it is extremely versatile. In rigid form, it is strong but lightweight, resistant to chemicals and fire and with superior dielectric properties.
In its higher grades, rigid mica sheet is perfect for creating specialist machine shapes for tooling applications, reducing heat transfer within equipment.
Manufacturing Parts for Manufacturing Tools
The UK manufacturing industry is evolving and thriving in different ways.
In the UK, manufacturing makes up around 11% of the country’s gross value added (GVA) as well as 705 of business research and development (R&D).
One of the challenges the UK economy has is to empower smaller businesses to grow into medium-sized companies with the ability to compete effectively on a global stage.
Some of the UK’s dynamic, specialist manufacturers are succeeding in making this step forward, but they are dependent on CNC machine tooling to help them do so.
CNC machining can make a big difference to production because of how it can streamline manufacturing processes.
However, this kind of advanced tooling also depends on the critical use of the right materials and design to ensure it can regulate heat as efficiently and effectively as possible.
There is, therefore, a causal link between effective thermal management and improved and sustained manufacturing success.
Modern machine tooling applications require much less human intervention, with automated operations, increased speed and programmable accuracy.
But this lack of intervention is dependent on minimising downtime and ensuring that the components and parts of the machine tools have the capacity to run uninterrupted while maintaining their precision.
As we have already seen, temperature changes can affect precision in tooling applications, and with the increasing sophistication of electronics driving CNC machine tooling, thermal management is more critical than ever.
Thermal Management Solutions for Tooling
Elmelin produces a range of mica sheet materials suitable for tooling applications. These include machined and punched parts, including customised fixtures and jigs for semi-conductors.
Rigid grade mica sheet also comes as complex machine parts such as washers, flanges, tubes, gaskets and discs.
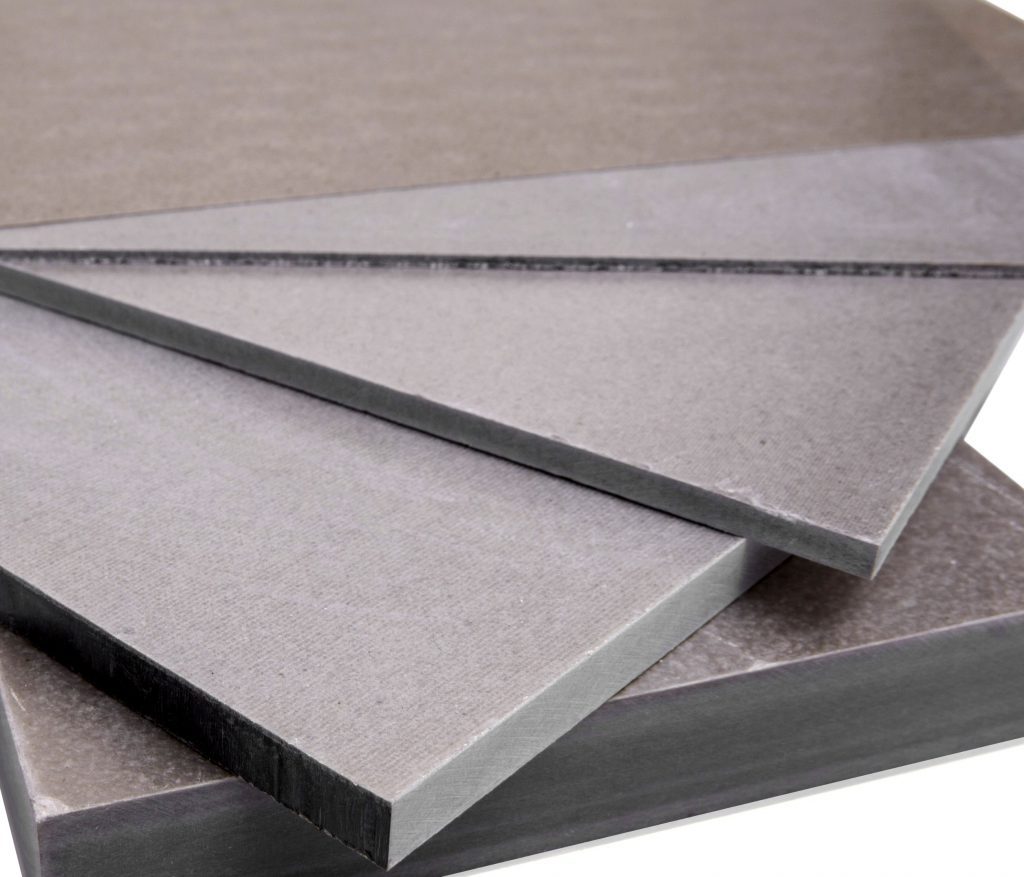
Alongside these products, we also have an advanced prototyping capability, which means we can offer expert support for manufacturing R&D, including specialist tooling.
For more information, please call us on +44 20 8520 2248, email sales@elmelin.com, or complete our online enquiry form. We’ll get back to you as soon as possible.